Laser Micro-machining The laser beam is characterized by the half divergence angle (θ= D/2f) and radius of beam waist, w For an ideal beam θw = λ/π(an invariant over the whole beam trajectory). A beam quality parameter is M2 number = (θw) / (λ/π) The minimum spot diameter of a beam δis given by – δ= (4/π) M2 λ(f/D). Laser beam machining. Materials: All materials Job: Drilling fine holes, cutting contours in sheets, cutting narrow slots. Electron beam machining. Materials: All materials Job: Drilling fine holes ULTRASONIC MACHINING(USM) Frequency: 20 KHz Amplitude: 15-20m. Power supply Transducer. Up-down vibration of tool. . To create this thermal gradient implies that a laser beam must traverse the workpiecemoving at such a speed that the thermal depth, z, is small compared to the workpiecedepth s0 1 1 2 = = t z Fourierno α t = interactio n time ME 677: Laser Material Processing Instructor: Ramesh Singh 8 1 / 1 2 0 2 0 2 0 2 0 2. Laser Beam Machining - Free download as Powerpoint Presentation (.ppt), PDF File (.pdf), Text File (.txt) or view presentation slides online. A brief description on LBM. Material removal process ppt, In the pad polishing process the material removal occurs due to the contact of the hard abrasive grains from the polishing suspension with the surface. This contact results in the wear of the sample’s surface. The simulation of the robot polishing.
Laser Beam Machining Seminar Report
The experimental and theoretical studies show that method performance will be improved significantly by the correct choice of optical device parameters, material parameters, and operative parameters. This seminar report reviews the analysis work administered thus far within the space of LBM of various materials and shapes. The Seminar Report discusses the experimental and theoretical studies of LBM to enhance the method performance. many modeling and improvement techniques for the determination of optimum ray of the light cutting condition are critically examined. The last part of this seminar report discusses the LBM developments and descriptions of the trend for future analysis.
Plasma-arc machining (PAM) employs a high-velocity jet of high-temperature gas to melt and displace material in its path. Called PAM, this is a method of cutting metal with a plasma-arc, or tungsten inert-gas-arc, torch. The torch produces a high-velocity jet of high-temperature ionized gas called plasma that cuts by melting and removing material from the workpiece. Temperatures in the plasma zone range from 20,000° to 50,000° F (11,000° to 28,000° C).
This article consists of the Plasma arc machining working principle, plasma arc machining diagram, process, advantages and Disadvantages of plasma arc machining, application of plasma arc machining.
What is Plasma
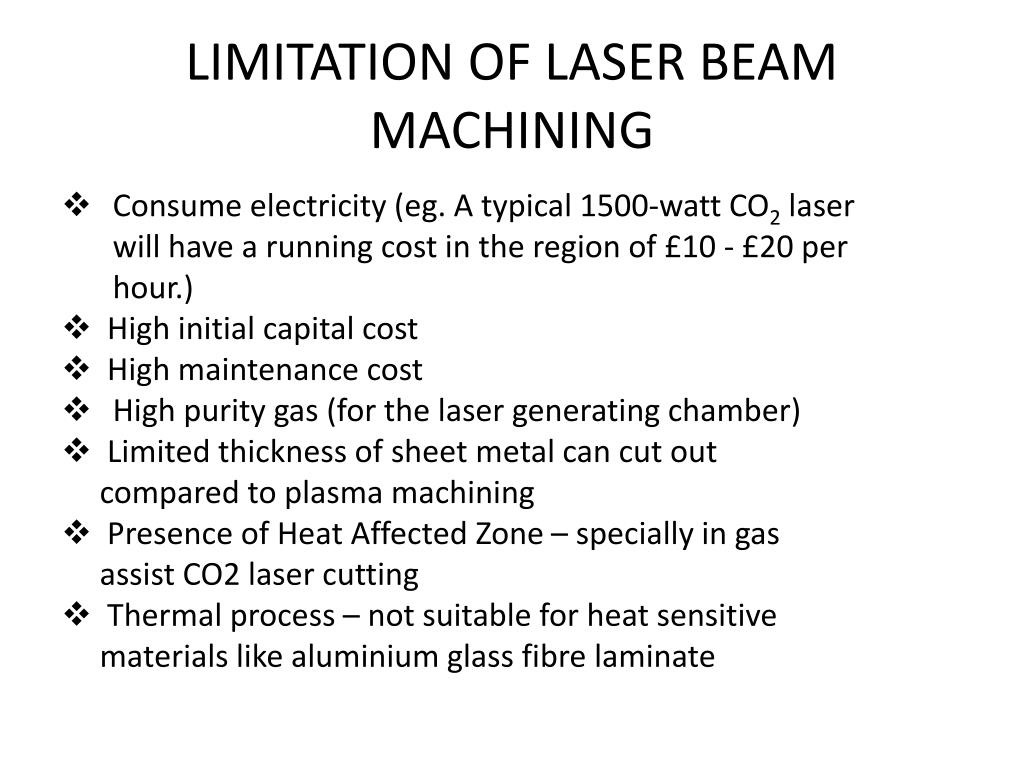
Solids, liquids, and gases are the three familiar states of matter. In general when solid is heated, it turns to liquids and the liquids eventually become gases. When a gas is heated to sufficiently high temperature, the atoms (molecules) are split into free electrons and ions. The dynamical properties of this gas of free electrons and ions are sufficiently different from the normal unionized gas. So, it can be considered
a fourth state of matter, and is given a new name, PLASMA’. In other words, when the following gas is heated to a sufficiently high temperature of the order of 11,000°C to 28,000°C, it becomes partially ionized and it is known as ‘PLASMA’. This is a mixture of free electrons, positively charged ions, and neutral atoms.
This plasma is used for the metal removal process. The plasma arc machining process is used for cutting alloy steels, stainless steel, cast iron, copper, nickel, titanium, and aluminum, etc.
Working Principle of PAM
In the plasma arc machining process, the material is removed by directing a high-velocity jet of high temperature (11000°C to 28,000°C) ionized gas on the workpiece. This high-temperature plasma jet melts the material of the workpiece.
Process Details of PAM
Details of PAM are described below.
- Plasma Gun
Gases are used to create plasma-like, nitrogen, argon, hydrogen, or a mixture of these gases. The plasma gun consists of a tungsten electrode fitted in the chamber. The electrode is given negative polarity and the nozzle of the gun is given positive polarity. The supply of gases is maintained into the gun. A strong arc is established between the two terminals anode and cathode. There is a collision between molecules of gas and electrons of the established arc. As a result of this collision, gas molecules get ionized and heat is evolved. This hot and ionized gas called plasma is directed to the workpiece with high velocity. The established arc is controlled by the supply rate of gases. - Power Supply and Terminals
Power supply (DC) is used to develop two terminals in the plasma gun. A tungsten electrode is inserted to the gun and made cathode and nozzle of the gun is made anode. Heavy potential difference is applied across the electrodes to develop a plasma state of gases. - Cooling Mechanism
As we know that hot gases continuously come out of nozzle so there are chances of its overheating. A water jacket is used to surround the nozzle to avoid its overheating. - Tooling
There is no direct visible tool used in PAM. Focused spray of ho0t, plasma state gases works as a cutting tool. - Workpiece
The workpiece of different materials can be processed by the PAM process. These materials are aluminum, magnesium, stainless steel, and carbon and alloy steels. All those material which can be processed by LBM can also be processed by the PAM process.

Construction Of Plasma arc Machining :
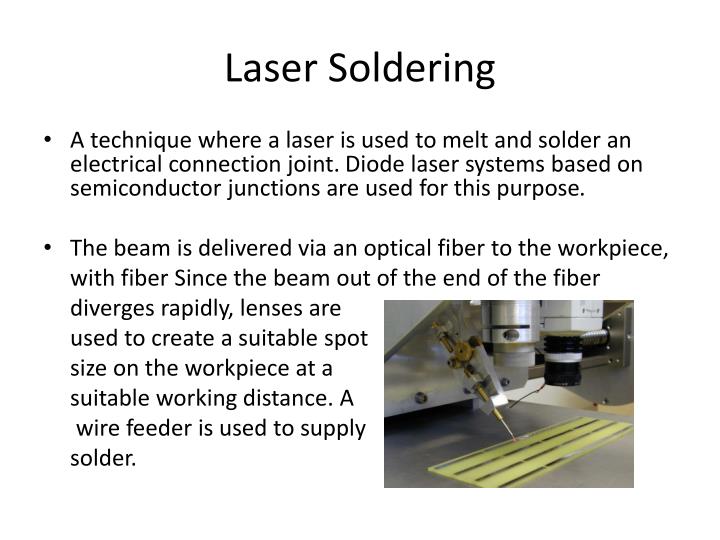
• The schematic arrangement of plasma arc machining is shown in Fig.
• The plasma arc cutting torch carries a tungsten electrode fitted in a small chamber.
• This electrode is connected to the negative terminal of a DC power supply. So it acts as a cathode.
• The positive terminal of a D.C power supply is connected to the nozzle formed near the bottom of the chamber. So, nozzle acts as an anode.
• A small passage is provided on one side of the torch for supplying gas into the chamber.
• Since there is a water circulation around the torch, the electrode and the nozzle remains water-cooled.
Working of PAM :
- When a D.C power is given to the circuit, a strong arc is produced between the electrode (cathode) and the nozzle (anode).
- A gas usually hydrogen (H2) or Nitrogen (N2) is passed into the chamber.
- This gas is heated to a sufficiently high temperature of the order of 11,000°C to 28,000°C by using an electric arc produced between the electrode and the nozzle.
- In this high temperature, the gases are ionized and a large amount of thermal energy is liberated.
- This high velocity and high-temperature ionized gas (plasma) is directed on the workpiece surface through the nozzle.
- This plasma jet melts the metal of the workpiece and the high-velocity gas stream effectively blows the molten metal away.
- The heating of workpiece material is not due to any chemical reaction, but due. to the continuous attack of plasma on the workpiece material. So, it can be safely used for machining of any metal including those which can be subjected to the chemical reaction.
ACCURACY
• Plasma arc machining is a roughing operation to an accuracy of around 1.4 mm with the corresponding surface finish. Accuracy on
the width of slots and the diameter of holes is ordinarily from ± 4 mm on 100 to 150 mm thick plates.
GASES USED IN PAM
The selection of a particular gas for use in this process mainly depends on the expected quality of surface finish on the work material and economic consideration. The gases used in this process, should not affect the electrode or the workpiece to be machined. The commonly used gases and gas mixtures are given in the following table.
Sr. No. | Gas or Gas Mixture | Material to be Machined |
---|---|---|
1 | Nitrogen - Hydrogen, Argon - Hydrogen | Stainless steel and non- ferrous metals. |
2 | Nitrogen - Hydrogen, compressed air | Carbon and alloy steels, cast iron. |
3 | Nitrogen, Nitrogen - Hydrogen, Argon - Hydrogen | Aluminium, Magnesium |
STAND OFF DISTANCE
Stand-off distance is the distance between the nozzle tip and the workpiece. When the stand-off distance increases, the depth of penetration is reduced. With an excessive reduction of the stand-off distance, the plasma torch can be damaged by the metal spatter. The optimum
stand-off distance depends on the thickness of the metal being machined and varies from 6 to 10 mm.
ADVANTAGES OF PAM
- It can be used to cut any metal.
- The cutting rate is high.
- As compared to the ordinary flame cutting process, it can cut plain carbon steel four times faster.
- It is used for rough turning of very difficult materials.
- Due to the high speed of cutting, the deformation of sheet metal is reduced while the width of the cut is minimum and the surface quality is high.
DISADVANTAGES OF PAM
1. It produces a tapered surface.
2. The protection of noise is necessary.
3. The equipment cost is high.
4. Protection of eyes is necessary for the operator and persons working in nearby areas.
5. Oxidation and scale formation takes place. So, it requires shielding.
6. The work surface may undergo metallurgical changes.
APPLICATIONS
1. It is used for cutting alloy steels, stainless steel, cast iron, copper, nickel, titanium, aluminum, and alloy of copper and nickel, etc.
2. It is used for profile cutting.
3. It is successfully used for turning and milling of hard to machine materials.
4. It can be used for stack cutting, shape cutting, piercing, and underwater cutting.
5. Uniform thin film spraying of refractory materials on different metals, plastics, ceramics are also done by plasma arcs.
CHARACTERISTICS OF PAM
- Metal removal technique: Heating, melting, and vaporizing by using plasma.
- Work material .-All materials that conduct electricity.
- Tool: Plasma jet
- Velocity of plasma jet: 500 m /s
- Power range: 2 to 220 kW
- Current: As high as 600 amp.
- Voltage : 40 – 250 V
- Cutting speed: 0. 1 to 7 m / min
- Metal removal rate: 145 cm3 /min
Some Questions and Answers Related to PAM
1. What is plasma?
When a flowing gas is heated to a sufficiently high temperature of the order of 1 l,000°C to 28,000°C, it becomes partially ionized and it is known as plasma.
Advanced Laser Machining
2. What is transferred arc type plasma?
In the transferred arc type process, the electrode is connected to the negative terminal of the D.C power supply, and the workpiece is connected to the positive terminal of a D.C power supply. So, more electrical energy is transferred to the work, thus giving more heat to the work.
3. What is non-transferred arc type plasma?
Laser Beam Welding Ppt
In non-transferred arc type, the electrode is connected to the negative terminal of a D.C power supply and the nozzle is connected to the positive terminal of a D.C power supply. When the working gas passing through the nozzle, a part of the working gas becomes heated, ionized, and emerges from the torch as the plasma jet. This plasma feeds the heat to the workpiece. This type of torches are used for non- conducting materials.
Laser Beam Machining Ppt Free Download
Related posts:
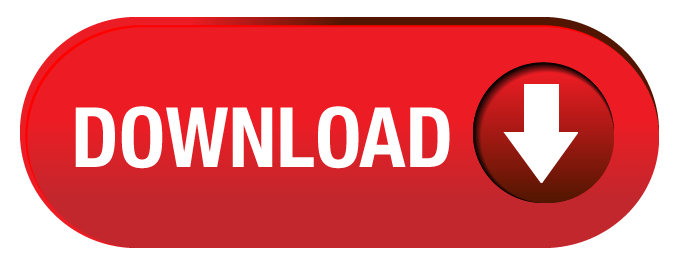